轻量化的产品和技术路线有哪些?轻量化趋势下的行业发展逻辑和机会是什么?市场空间怎么看?
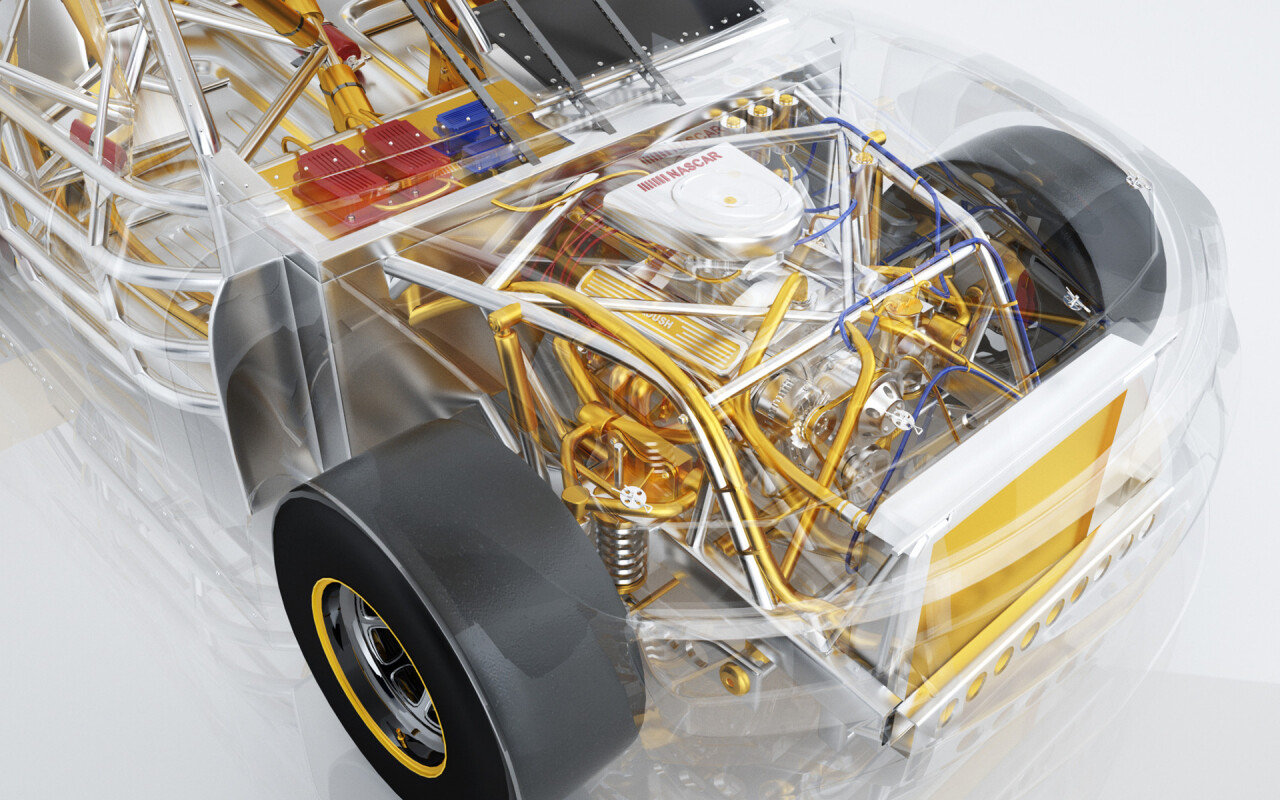
编者按:本文来自 昆仲资本,创业邦经授权发布,头图来源摄图网
安·兰德(Ayn Rand)在她最著名的小说《阿特拉斯耸耸肩》(Atlas Shrugged)中描绘了一款跨时代的“里尔登”合金产品——使用这款产品造出的火车,时速可以由60公里/时,提高到100公里/时,车身重量是原来的1/5,效率可以提升10倍。
这本小说所预测的趋势正在六十多年后逐渐成为现实:随着“双碳”目标持续推进使得汽车行业节能环保需求日益迫切,各国对汽车节能和排放环保已经达成共识,倒逼汽车朝着轻量化的方向发展。
有研究显示:燃油车可通过提高轻量化减少燃料消耗以及降低排气污染(若整车重量降低10%,燃油效率可提高6%到8%);新能源车则可通过提高轻量化提升新能源车加速性能及续航里程(车身减少100kg重量,动力电池续航能力就会增加 10-11%)。
那么轻量化的产品和技术路线有哪些?轻量化趋势下的行业发展逻辑和机会是什么?市场空间怎么看?
从目前国际通行的研究方向来看,轻量化的技术方向包括:“结构轻量化、材料轻量化、工艺轻量化”三个维度,但是整体是在围绕车用材料进行升级与完善:
当前的主要汽车轻量化措施主要是采用轻质材料。在各类轻量化材料中,铝合金的成本仅高于高强度钢,但远低于镁合金、塑料及碳纤维。同时,铝合金密度约为高强度钢的1/3,与镁合金相当,能够实现有效的轻量化。
由此,考虑到成本、减重性价比及安全性能等综合因素,铝合金材料成为了当前应用最为广泛、渗透最快的材料之一。
此外,使用铝合金材料也更为环保。根据头豹研究院数据,采用铝制材料为主的汽车,所排放的温室气体总量为30371kg,低于常规材料的33270kg和高强度钢的31189kg。
但是,目前车身结构件铝合金渗透率相对较低,主要原因包括:
但如果说未来铝合金结构件渗透有望从底盘+三电提升到整个白车身的话,则单车提升价值约在16000元。
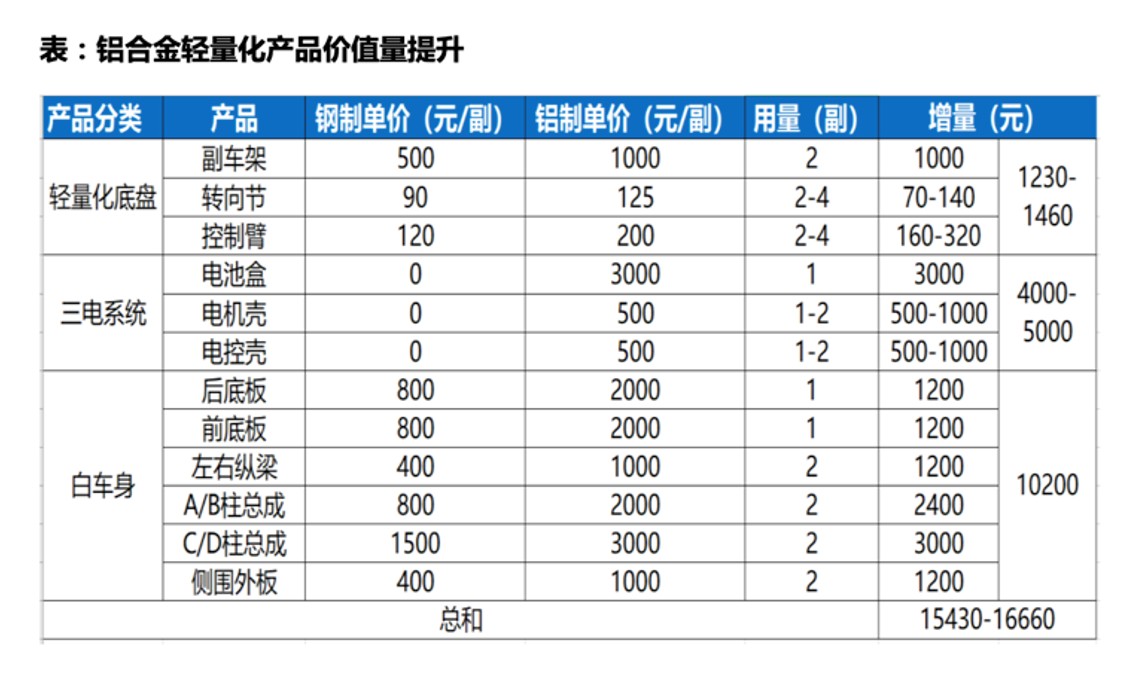
由此可见,乘用车铝合金市场空间广阔,2025年车均用量接近翻倍(139kg-350kg)。那么根据测算,2025年国内车用铝合金市场空间约为1362亿元,2020-2025年CAGR为17.1%,其中三电系统/轻量化底盘/车身结构件2020-2025年CAGR分别为62%/25%/72%。
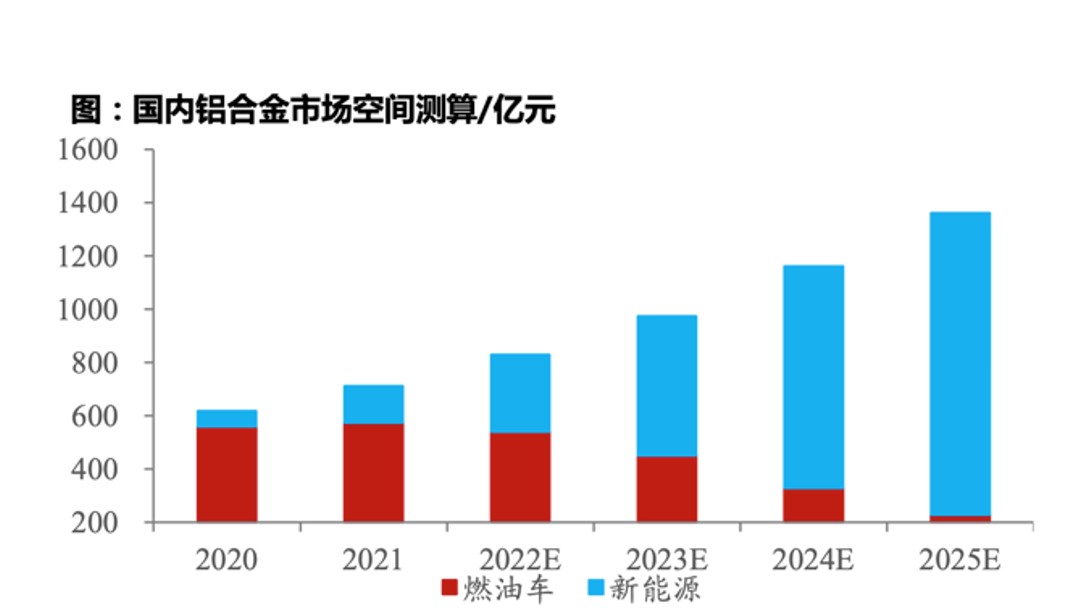
但是铝合金的制约也很明显:如果采用铝合金替代钢材,白车身确实可降重1/3左右。以奥迪A8为例,因采用全铝车身,白车身重量仅为215kg。但由于铝金属导热系数大,易造成焊缝性能下降、合金表面氧化层污染电极的问题,并且铝的热膨胀系数高易导致零件变形大。
仍以奥迪A8为例,其车身制造需要包括MIG焊、远程激光焊等在内的14种连接工艺,工艺复杂度远高于以电阻焊为主的钢制白车身。
由于压铸件在汽车领域的用量占比最高,因此,在铝合金的大趋势下,压铸工艺也有待变革。
在说在压铸之前,我们简单介绍下汽车制造传统四大工艺:冲压、焊装、涂装、总装。
冲压:作为首个工序,冲压工序把来料板材通过专用模具加工成特定形状的零件。
焊装:冲压加工出来的白车身零件被人工或者设备自动放入特定的焊接工装上,焊接机器人或者工人通过焊接设备把不同的冲压零件焊接成分总成,然后将分总成焊接成总成,最后总成被焊接成完整的白车身。
涂装:白车身从焊装车间出来之后将会进入涂装车间,白车身在涂装车间会经过电泳、中漆、面漆3个处理工序。
总装:总装是汽车四大工艺的最后一个工艺。总装线主要有内饰线、底盘线、 外饰线等。油漆车身从涂装车间出来之后会进入总装线,会进行车门、线束、安全气囊、仪表板、前后桥、发动机、轮胎等各种外饰、内饰、电子部件等零部件的安装。
可见,相比较传统的冲压+焊接工序而言,如果采用一体化压铸的方式,那么部件就能一次成型,内部不需要额外连接,因此焊接、铆接、涂胶工艺的使用大幅减少,从而就能降低生产线上的人工成本,及焊接、涂胶机器人的成本。
一体化压铸车身是轻量化技术的升级,可以减少车身零件数量、简化供应链环节、提升原材料利用率,进而使得汽车组装效率大幅提升。
当前一体化压铸变革主要应用于新能源汽车型开发,特斯拉是一体化压铸车身应用的先锋,大型压铸机将 Model 3后底板所需的70个零部件,通过一体压铸,整合成 Model Y上只需要2个零件。同时,一体化压铸在电驱动系统上也有所体现,随着电驱系统集成更多功能,电驱动壳体的设计也将从独立式走向集成式一体化设计。如今,蔚来、小鹏、理想也紧随特斯拉布局一体化压铸。
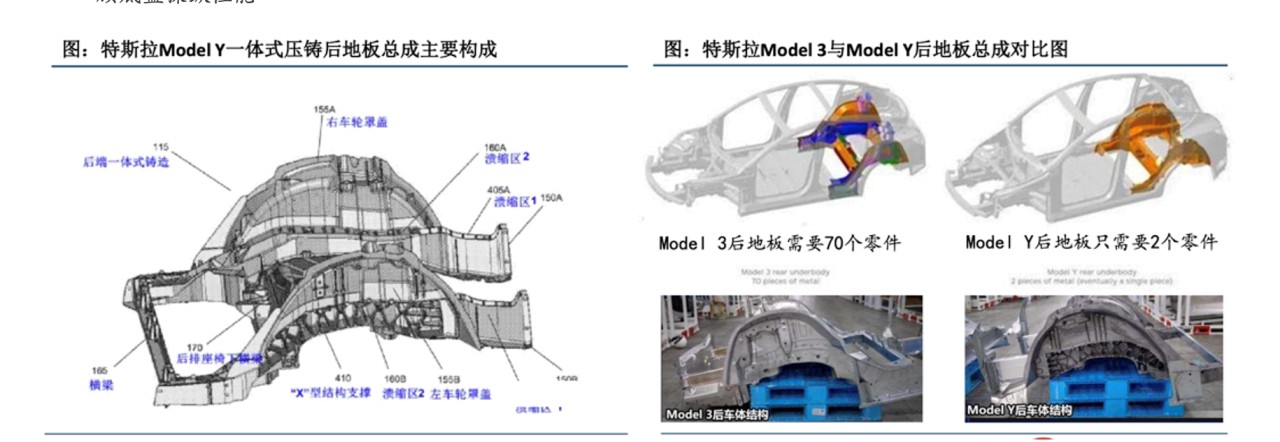
此外,一体化压铸不仅可以应用在车身和底盘结构件,在电驱动系统上也有所体现。电驱动系统设计经历了独立式、二合一、三合一和多合一的发展阶段。
目前,比亚迪E平台3.0上采用了前驱感应异步电机+后驱永磁同步电机的技术方案,实现了全球首个八合一动力总成;华为也推出了DriveONE多合一电驱动系统,集成了电机控制器(MCU)、电机、减速器、车载充电机(OBC)、电压变换器(DC/DC)、电源分配单元(PDU)及电池管理系统主控单元(BCU)七大部件。电驱系统集成更多功能是大势所趋,电驱动壳体的设计也将从独立式走向集成式设计: 从分体式简单集成,即减速器、电机和电控有各自独立的壳体设计,到三大件壳体一体化。
一体化压铸技术的壁垒主要在大型压铸机、压铸模具、材料配方和压铸工艺这几方面。
大型压铸机行业进入门槛高,其“设计—试验—设计”周期非常长,前期需投入大量时间成本,目前掌握此类重型压铸机的产商只有以国内力劲、伊之密,国外布勒为代表的为数不多的压铸机生产商。
材料配方是一体化压铸技术的核心竞争点。一体化压铸对铝合金材料的性能提出更高要求,压射的合金熔液需具备良好的流变性能、较小的线收缩率和较小的凝固温度区间。复杂的材料配方大幅提升了一体化压铸的技术门槛,成熟掌握合金原料配方的企业在一体化压铸市场具备明显优势。
一体化压铸对模具的强度及韧性要求更高。与其他铸造工艺相比,压铸工艺特性主要体现在“高速充型与高压凝固”上,在温度、真空、成型方案、工艺参数、后处理等方面都比传统铸造工艺存在更高要求。相比普通压铸的模具,一体化压铸模具更复杂,对强度和韧性要求更高。
一体化压铸工艺复杂,全工艺要素均有较高要求。压铸工艺对生产合格的汽车结构件十分重要,正确地选择压射模式、压射参数等有利于减少压铸件中的缺陷。压铸件中的气体有相当一部分来自金属液在压室中的预充填阶段,所以应充分注意优化慢压射阶段的压射模式,避免金属液在压室中卷入气体。
昆仲资本持续关注汽车轻量化产业链的投资机会,我们认为创业公司的机遇在于:材料>部件>模具及设备。
从产业链格局上看,部件环节由本土公司主导,压机处于供不应求状态,免热材料本土厂商正逐步突破。
设备及模具方面:压机环节目前供不应求,力劲在交付、订单及在研项目层面较为领先,布勒与海天均有6000吨压机交付; 模具环节,广东型腔已获得较多Tier1(或主机厂)订单,文灿雄邦具备自制能力;
材料方面:通常材料厂商或科研院所与Tier1(或主机厂)共同研发,前期美国铝业已实现批量供应,本土企业立中集团已有产品量产;
部件方面:目前主要以本土企业为主,虽然有特斯拉等主机厂自制,但长期看随产业链成熟后我们认为仍然是Tier1主导。
目前汽车轻量化的技术壁垒在于材料和部件: 一体化压铸车身结构件具备大尺寸、薄壁、结构复杂等特点,对强度、延伸率等要求较高,需用免热处理材料、高真空压铸工艺等,具备较多know-how,同时一体化使得资产壁垒显著提升。
参考文献:
本文为专栏作者授权创业邦发表,版权归原作者所有。文章系作者个人观点,不代表创业邦立场,转载请联系原作者。如有任何疑问,请联系[email protected]。