改变从边缘开始,国产的协作机器人从汽车制造业的部分环节,率先撕开了一个口子。2021年,国产协作机器人在中国的占有率超过90%以上。
在汽车制造业,“国产的协作机器人正在完成对于国际品牌的替代,这是竞争的结果。”上海节卡机器人科技有限公司副总裁常莉对第一财经记者表示。
汽车制造业是工业机器人主要的应用市场,不过该领域的国产机器人占有率很低,目前不足10%。这背后的原因在于,相较于家电等产业,汽车制造业对机器人的技术和稳定性有更高的要求,且国外企业发展更早而占得先机。
协作机器人是机器人的一个细分品类。有别于大功率、高成本、需要物理围栏的传统工业机器人,协作机器人被设计成可以在协作区域内与人直接进行近距离交互,有着部署成本低、易于上手等优点。改变从边缘开始,国产的协作机器人从汽车制造业的部分环节,率先撕开了一个口子。
边缘突破
李进是一家传统工业机器人厂商相关负责人,主要服务于汽车客户。
汽车行业客户通过招标方式寻求系统集成供应商进行合作,这将导致:一方面,客户对工业机器人有高标准要求,可以指定机器人品牌,指定品牌大多为国外机器人品牌;另一方面,招投标的方式让系统集成商更加“内卷”,都希望拿出高性价比方案,因而大多采用国际机器人产品。
“对于产线应用工业机器人的选择,部分情况是客户指定采购,部分情况是公司依据客户生产要求自行采购。”李进告诉第一财经记者,在采购方面,公司采用“以产定购”模式,确定所需原材料,包括螺柱焊机、工业机器人本体、焊枪、涂胶设备等标准设备。
汽车产业是最早应用自动化和部署机器人的行业。在中国市场,本土的机器人还没有能力实现对整车企业的正面突破。《2021中国工业机器人产业发展白皮书》显示,国产机器人在不同行业的占比情况中,汽车制造业用工业机器人的国产占有率最低,不足10%。
目前国内的协作机器人能实现的是应用于汽车生产的部分环节,比如总装。
一辆汽车生产出来大致需要经过5个车间:冲压、焊接、喷涂、总装、动力总成。前三个车间对于传统工业机器人的使用量较大;后两个车间可以用到协作机器人。
“前三个车间(冲压、焊接、喷涂)由于是产线式的生产方式,对于机器人本身的技术、汽车整车的制造工艺要求较高,基本已实现自动化。”常莉表示,上述三个车间国产工业机器人的占有率是比较低的,更多的是以国际品牌的第一阵列(比如发那科、ABB、安川、库卡)为主。
后两个车间(总装、动力总成)工序较灵活,引入协作机器人和工人并肩工作,提高工厂整体的生产效率。
汽车零部件行业发展紧跟汽车工业,汽车零部件因其所适配的车型不同,产品材质、形状、大小、重量等各异。大部分厂商选择使用协作机器人提升质量和生产柔性,以满足用户的需求。协作机器人已广泛应用于汽车零部件的浸涂、上下料、装配等工序。
国产的协作机器人已经可以打入跨国大厂的制造环节。丰田汽车目前唯一的协作机器人供应商是上海的节卡机器人。
“在工业4.0时代,丰田需要建立一个销售驱动的系统,即获取更多的经营数据、经营定制化,进而推动后端的生产。丰田对汽车生产场景也做一个变革,比如派单、生产、物流、销售网络等环节。”常莉表示,基于生产模式的变革,丰田认为协作机器人能够更好的适应柔性、智能的生产场景。
当前,节卡机器人主要应用于丰田设立在中国、日本等地的工厂,运行于动力总成、总装、汽车零部件制造等车间。
《2022年中国协作机器人技术发展报告》显示,2021年,国产协作机器人在中国的占有率超过90%以上。2021年国产协作机器人销量达15300台,同比增长45.7%,实现销售额突破15亿元。
常莉表示,从供给端看,在协作机器人领域,中国的厂商要远多于国外厂商,主要是行业发展的土壤在中国;从应用端看,以丰田、本田、大众为代表的大客户每年的需求呈现倍速增长,在早期探索阶段,他们也是使用国际的品牌,然而随着行业的发展,对于产品的理解、需求不断加深,公司的发展、效率的提升,产品质量、服务有着严苛的要求,面临着成本的上涨,越来越多的客户从原先的国际品牌(比如,优傲)转而选择国产品牌。
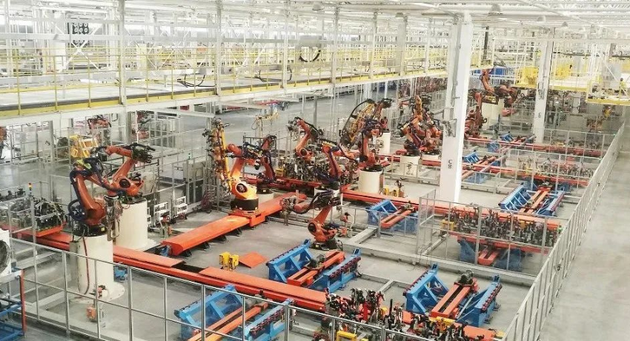
新能源车带来的机会
新能源汽车的大发展,给机器人的应用带来一些变化。
比如,以特斯拉为代表的部分车企开始用一些大型的铸造机器来做一体化的车身。这一工艺使得汽车车身上的焊接点更少,焊接用工业机器人的使用也相应的减少了。
“生产工艺大体类似,不同点在于一些工艺点的改造上面,比如新能源车的车身轻量化、从点焊变成了激光焊接。随着工艺流程的改变,焊接环节的机器人数量会减少,这是必然的。”常莉表示。
李进所在的公司目前主要目标是推进在新能源领域应用突破的项目。
“由于终端用户对新能源汽车的需求标准不断提升,新能源汽车的制造工艺因车身材料、安全性、稳定性、节能性等要求而提升制造工艺标准,这对工业机器人的品质,即:精度、速度、刚度等提出更高要求,倒逼国产机器人不断提升产品质量。”李进表示,新能源属于近期热门新兴行业,自动化需求旺盛且个性化明显,需持续开发新的机器人应用技术与制造工艺。
新能源车的关键部件是电池,后者的自动化提升过程也将为国产机器人带来机会。
根据中国汽车工业协会的统计,2021年全国氢燃料电池汽车产销数据分别为1777辆和1586辆,同比增加48.2%和34.7%。2015年至2021年,全国氢燃料电池汽车累计产量和销量分别是9237辆和8938辆。
燃料电池业内人士陈芳对第一财经记者表示,国家非常重视氢能产业关键技术的自主化水平提升,目前这些关键技术大部分已经实现国产化,但为了不断提升产品性能指标如稳定性、耐久性,需要进行大量的测试,在生产环节,也需要根据实际情况不断进行调整。虽然很多燃料电池企业规划了较大的产能规模,也投入了产线,但从成本和实际需求出发,一些环节的自动化程度当前并不太高。
陈芳表示,燃料电池汽车目前主要发力在商用车领域,在相关补贴政策推动和国家双碳战略落实的背景下,该行业规模化采用机器人自动化产线,只是时间问题。
新的领域为国产机器人开拓出新的市场可能,尤其是协作机器人。在常莉看来,协作机器人不存在传统工业机器人那么大的技术瓶颈。
“影响中国机器人产业瓶颈的主要是在传统的工业机器人;对于协作机器人,只有10年左右的历史,中国的工厂拥有大量应用的场景,与国外企业相比不存在需要突破的瓶颈。”常莉认为。据她介绍,节卡机器人的核心部件,比如减速器,使用的是国内企业绿的谐波(688017.SH)的产品。
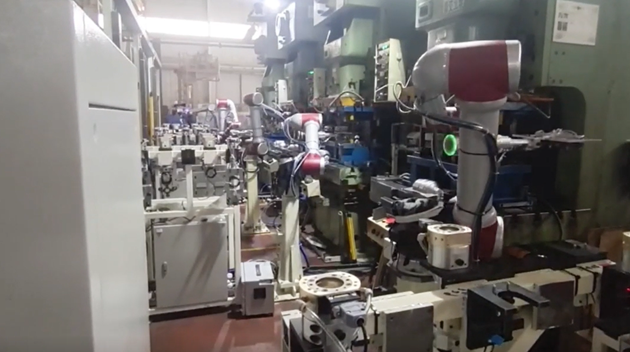
向谁借鉴
就传统工业机器人而言,“关键零部件占据工业机器人本体70%的生产成本,国产机器人品牌的核心零部件依赖进口,国产核心零部件目前在质量稳定性、可靠性等方面还不能满足高性能需求。”李进表示,他所在公司机器人本体的核心零部件还是从国外引进的。
常莉认为“打铁还需自身硬”,国内的机器人企业首先要做好产品的打磨,同时要重视机器人产业链、生态的共商共建。
“协作机器人需要具备力传感技术、视觉识别、控制系统、机器人末端执行器等多种产品、应用技术。”常莉分析说:“更重要的是需要将技术结合更多的生态,包括终端客户的工艺部门、自动化部门一起进行场景的突破和打造。”
去年,工信部等十五部门联合发布了《“十四五”机器人产业发展规划》,《规划》中提到,机器人行业要“补齐产业发展短板。推动用产学研联合攻关,补齐专用材料、核心元器件、加工工艺等短板,提升机器人关键零部件的功能、性能和可靠性;开发机器人控制软件、核心算法等,提高机器人控制系统的功能和智能化水平。”
要想完成国产工业机器人升级,李进认为,还需要持续攻坚在减速器、控制器及伺服系统等领域的核心技术,提升工业机器人核心零部件的自制率;健全人才保障体系,支持高校和科研院所培养高端人才,从而推进机器人应用与机器人自主研发;深化国际交流,鼓励国外企业在华设立研发机构,推进机器人产品和解决方案“走出去”。
德国和日本是传统的制造业强国,两国的机器人产业均有值得国内企业借鉴的地方。
“日本是机器人大国,汽车、电子、自动化产业比较发达,在亚洲,乃至世界范围都是典型的市场。德国作为工业4.0的标杆,自动化技术、工业巨头来源于此,比如施耐德、西门子。我们希望能够去到产业最发达的地方,利用当地的人员、扎根下去,服务当地产业、客户。”常莉表示,节卡的日本、德国公司的技术人员占比约为60%。
机器人属于技术密集型产业,节卡在日本、天津、上海分别设立研发中心,三者侧重点各有不同。该公司位于日本的研发中心侧重于技术,比如机器人本体上感知技术的研发、应用;天津的研发中心聚集于客户周围,侧重于工艺、应用的研发;上海的研发中心侧重于产品研发的落地。
近年来,协作机器人发展迅猛,行业已经有低端重复性建设的苗头。
“任何一个有前景的行业都会吸引很多资本、玩家进入,肯定会存在重复性建设的问题。检验一家公司产品好坏直接看其产销量即可。国内做协作机器人的厂商约为200家,产量达到1000台以上的厂商就已经很少了,可能不到10家。”常莉表示,协作机器人的优胜劣汰已经开始了。
(应受访者要求,李进、陈芳为化名)