原标题:不用高温也能搓出一颗玻璃球?Science最新研究让低温注塑玻璃成 来源:量子位
不知道大家有没有看过类似“玻璃弹珠制作”的视频。视频中,工人师傅需要将玻璃原料高温加热后,在其处于流体状态下快速塑形。虽然隔着屏幕,但我们也会为操作师傅捏一把汗,毕竟这明晃晃的亮度,看着就很烫!
明敏 发自 凹非寺
量子位 报道 | 公众号 QbitAI
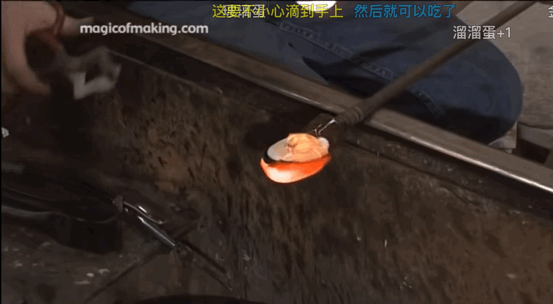
不过,Science一项最新研究表明,现在低温条件下可以注塑玻璃了!
德国弗莱堡大学Frederik Kotz和Bastian E. Rapp等人提出了一种使用二氧化硅纳米复合材料的高通量注塑工艺。
他们将低温注塑成型工艺(IM)与水基脱脂、低温烧结工艺相结合,开发出一种可以与注塑成型技术兼容的新型玻璃加工技术,能够快速批量生产高精密度、表面光滑的玻璃制品。

加工玻璃,没那么简单
这项技术的突破,可以说解决了目前玻璃加工产业的核心难点。
首先,高温熔融、浇铸一直以来都是困扰玻璃加工行业的难题。
1500℃以上的高温要求,一方面使得加工过程中产生能耗巨大(据估算每吨玻璃加工需要消耗5~6兆焦耳能量);另一方面在一定程度上限制了玻璃工业化加工的产能和效率。
其次,玻璃微观形貌加工多采用氢氟酸、激光蚀刻等方式,其制备过程危险、操作难度高、对环境污染大,能加工的形状和产量也会受到一定限制。
如何实现?
而Markus Mader等人采用低温注塑成型工艺(IM)与水基脱脂、低温烧结工艺相结合的方案,刚好解决了以上难题。
技术核心——注塑成型工艺(IM)是一种适用于工业化生产的快速加工技术,它通过把熔融的原料加压、注入、冷却、脱离,最终制作成一定形状的半成品。
此前这一技术多用于聚合物的加工制作,这一次研究人员突破性地将其应用在了玻璃加工上。
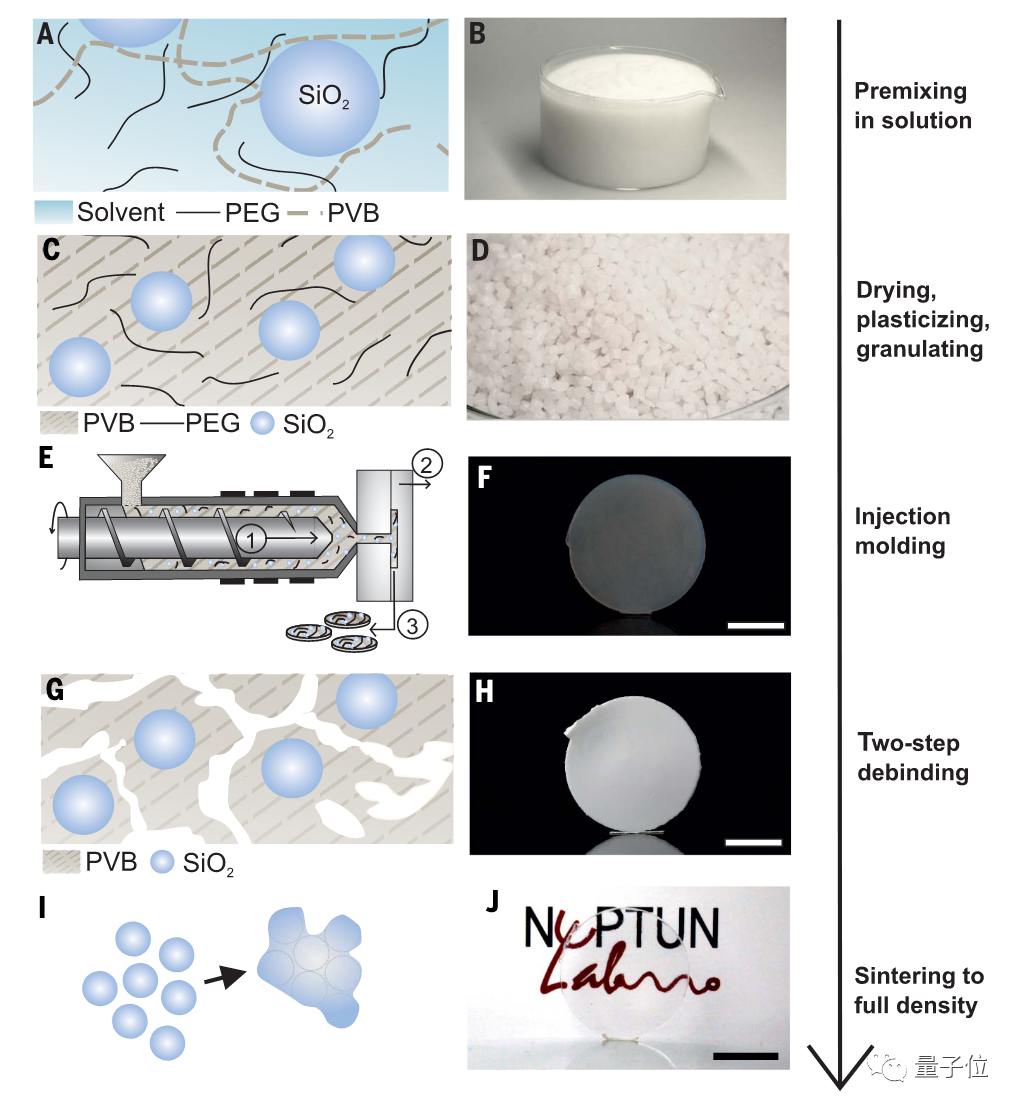
首先,研究人员将二氧化硅纳米粉、乙烯醇缩丁醛(PVB)溶液、乙烯醇缩丁醛(PEG)溶液预混合, 通过蒸发,得到了热塑性二氧化硅复合材料。
然后使用双螺杆挤出机将得到的材料塑化并挤出,得到颗粒状的原料;
随后在130°C、700 ~ 1000bar特定压力下注塑成型,得到了生坯部分;
将生坯先浸泡在40°C的水中,以脱去材料中的PEG,之后再用高温除去残余的粘合剂;
最后在1300°C的真空环境下烧结得到高质量的透明熔融石英玻璃。
由于采用了优化的两步脱脂程序,注塑成型的生坯零件(尺寸小于2毫米)转换为透明熔融石英,总共只需要24小时。
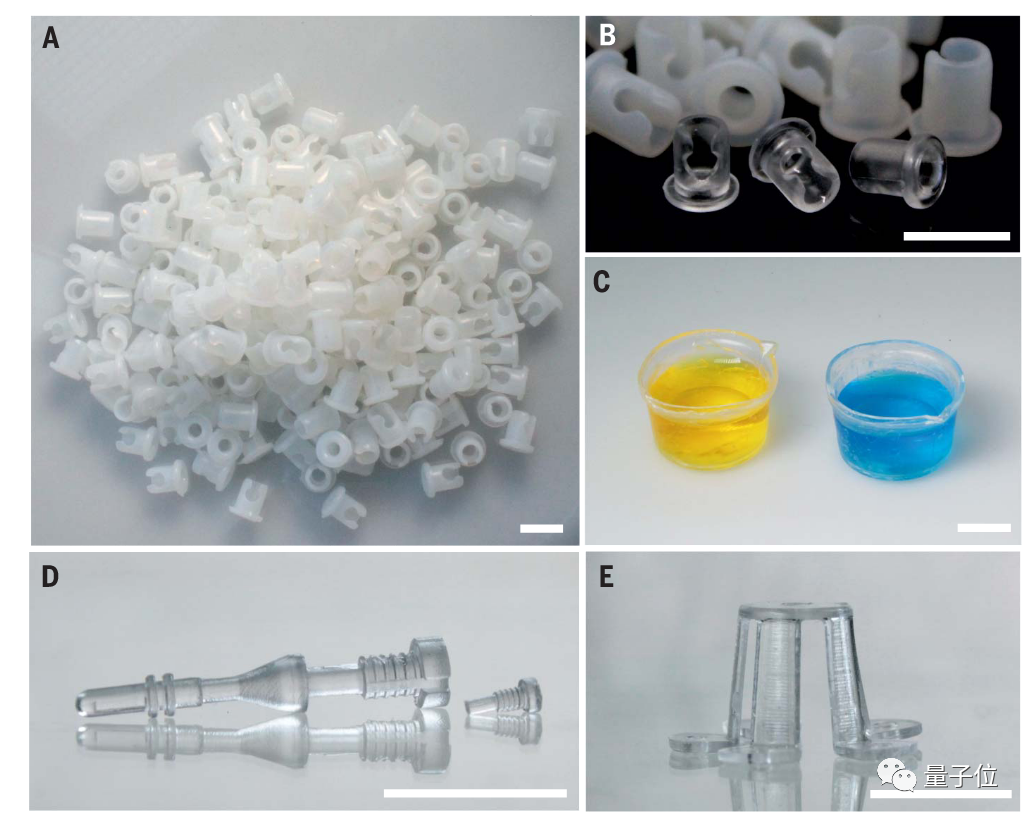
此外,研究人员进一步使用该技术艺在商用注塑机(Babyplast Christmann)上进行的高通量制造。
结果发现,即使以低至20秒的循环时间对二氧化硅纳米复合材料进行全自动注塑,也可以在工业生产水平上生产复杂形状的熔融石英零件。
在18分钟生产出了200多个零件,也就是说每5秒便能生产一个玻璃组件!
不仅如此,以上整个加工过程的能耗不到传统加工工艺的60%;而且由于脱脂过程不是在高温环境下进行,过程中使用的粘合剂还能回收利用。
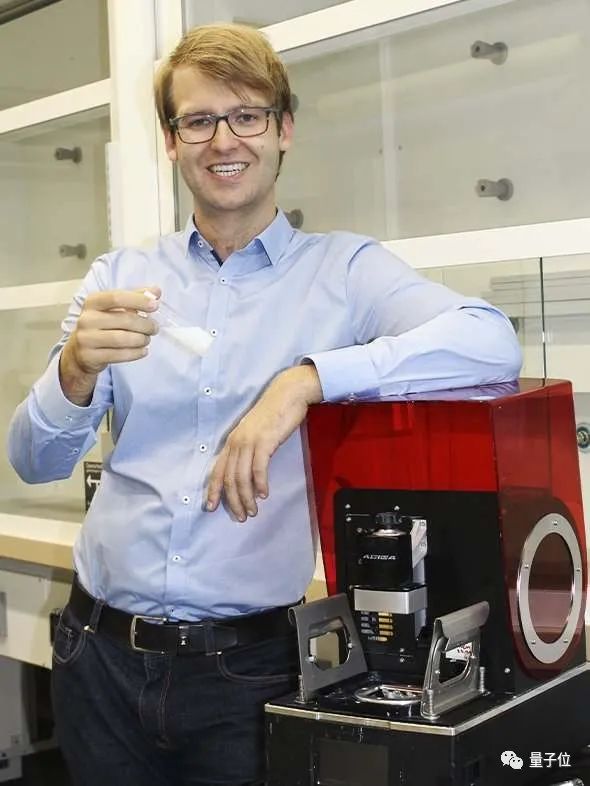
研究者Frederik Kotz说:“这一方法最终可以得到任意形状的高纯硅玻璃。”并表示这些玻璃部件最终还具有商业电信设备和化学反应堆所需的光学和化学特性。
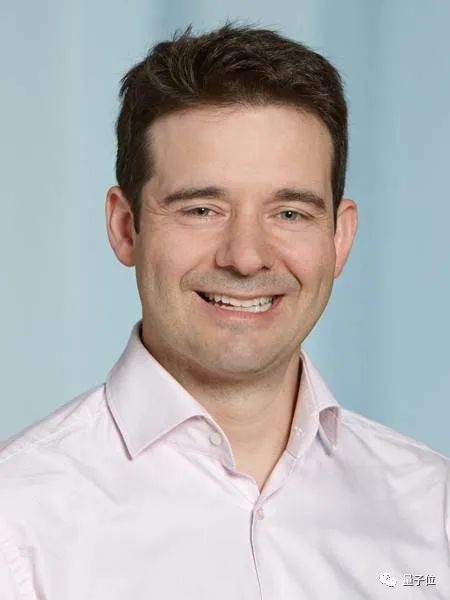
苏黎世联邦理工学院材料学家André Studart则表示这一方法可以引发出更多新的idea。
不过他提出这种大规模生产玻璃部件的新方法仍然面临一个瓶颈:脱掉PEG过程需要持续数天,以确保玻璃部件不会开裂。
”如果加快这一进程,玻璃的注塑成型就会像塑料一样流行起来!“