◎科技日报记者 代小佩 操秀英
在镇海炼化厂区内,一只白鹭悠然飞过一栋深蓝色的厂房。
厂房里,我国首套生物航煤工业装置,正在演绎“地沟油”飞上天的绿色传奇:每年能“吞”掉大约10万吨“地沟油”,再“吐”出4万吨至5万吨清澈的生物航空煤油。
8月初,记者来到这段传奇开始的地方——中国石化石油化工科学研究院(以下简称石科院),该院高级工程师渠红亮拿出他保存的近百篇报道和图片,向记者讲起我国生物航煤从无到有的故事。
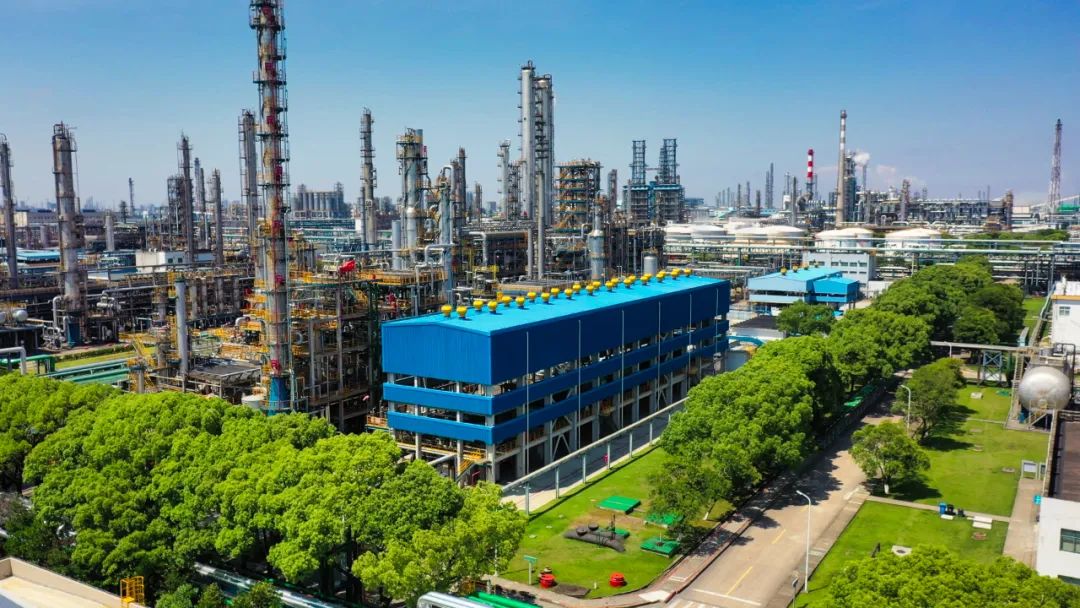
“要谈判至少得拿出筹码”
生物航煤是以可再生资源为生产原料的航空煤油。与传统的石油基航煤相比,生物航煤全生命周期二氧化碳排放可减少50%以上。2008年左右,美国、芬兰等国已成功开发生物航煤工业装置。
为响应我国节能减排号召,2006年,石科院开始了研发生物航煤的探索。
两年后的一条重磅新闻加速了这一进程。
“2008年,欧盟宣称,从2012年开始对所有入境航空公司征收航空碳排放税。”时任石科院副院长聂红回忆,如果这一政策实施,我国航空公司要在2012年至2020年间向欧盟缴纳约176亿元人民币。
面对天价“买路钱”,包括中国在内的多国提出反对意见。“我们很清楚,要谈判至少得拿出筹码。”聂红说。
技术成为最大的筹码。
但生产生物航煤的关键技术无疑是各公司的商业机密,我国科研团队只能从零开始、自主创新。“这是我们义不容辞的责任。”聂红和团队明确目标:一定要在欧盟征收碳税之前拿出我们自己的生物航煤产品!
石科院调集一半以上的研究室进行技术攻关。
彼时,美国生物航煤的原料主要是大豆油,芬兰则是菜籽油。“很显然,这两种原料都不适合我国。”石科院临氢工艺研究室副主任习远兵回忆。
可选项并不少,菜籽油、棉籽油、棕榈油,以及酸化废油、俗称“地沟油”的餐饮废油等都可作为原料。不过在我国,“地沟油”来源更广、成本更低。“我国每年消耗几千万吨食用油,如果把餐饮废油变成航空煤油,不仅节能减碳还降低了‘地沟油’回到餐桌的可能,利国利民。”习远兵说。
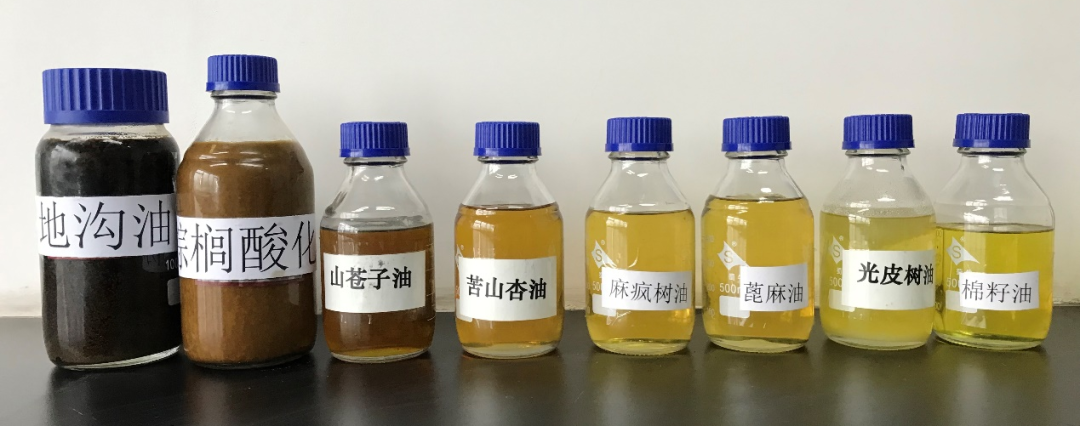
与动植物油相比,“地沟油”存在收集困难、杂质种类多且含量高等棘手问题。研发团队决定迎难而上。
“确实有一夜愁白头的时候”
要研制什么样的生物航煤?研发团队没见过,没头绪。
“我们就对标石油航煤来研制,把‘地沟油’变成与石油基航煤基本一致的组分。”渠红亮分析。
可生物航煤和石油基航煤的原料在组成上区别很大。石油主要由碳、氢两种元素组成,含氧量低于0.1%;而“地沟油”等生物油脂由碳、氢、氧3种元素组成,且含氧量高达10%—15%。氧分子直接影响炼化装置催化剂的活性和稳定性,如何除掉这些氧考验着团队。
加氢精制是炼油过程中脱氧、去杂质的重要技术手段。但生物油脂含氧量多,要加的氢也成倍增加。这就导致加氢精制过程中产生的总热量巨大,造成反应器温升过大,最高温累积可达500℃以上,远超反应器的承受力。
“控制反应温度的方法没有前车之鉴,只能大胆地试、去闯!”石科院加氢催化剂研究室主任杨清河说,大家基本上天天泡在实验室,为一些技术细节反复做实验,直到结果出来才休息,“确实有一夜愁白头的时候”。
最终,他们创新研发出专用催化剂和工艺,使得催化剂的脱氧活性、选择性和氢耗可调,反应器温升得到有效控制,并经过工业规模装置示范验证。
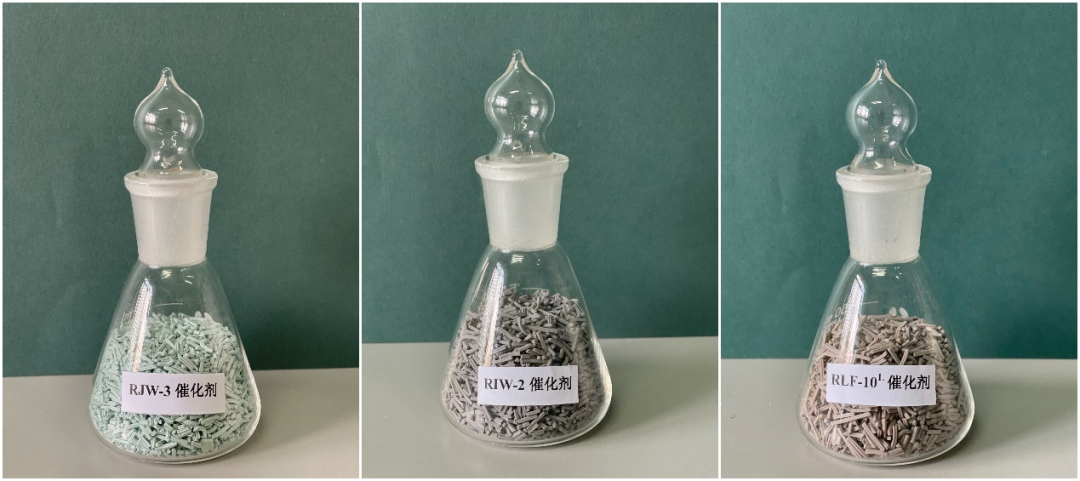
2011年12月,中国石化在镇海炼化杭州石化生产基地生产出生物航煤产品“1号航煤”。
2013年4月24日凌晨,一架“喝”了“1号航煤”的客机在上海虹桥机场试飞成功。中国成为世界上第4个拥有生物航煤自主研发生产技术的国家。
“我们要把生物航煤技术储备好”
“地沟油”变航空煤油,这只是第一步。从实验室到产业化,还有很多关要过。
为实现我国生物航煤规模化生产,中国石化要求镇海炼化打造一套生产能力为10万吨每年的生物航煤装置。
镇海炼化开始了大型改造工程。镇海炼化炼油四部生产经理李成刚告诉记者,他们共拆除报废设备104台、管线6000米,保护性拆除设备14台、管线300米,提出图纸优化建议300多条、现场比对资料180多份,提出审图建议超过1000条。
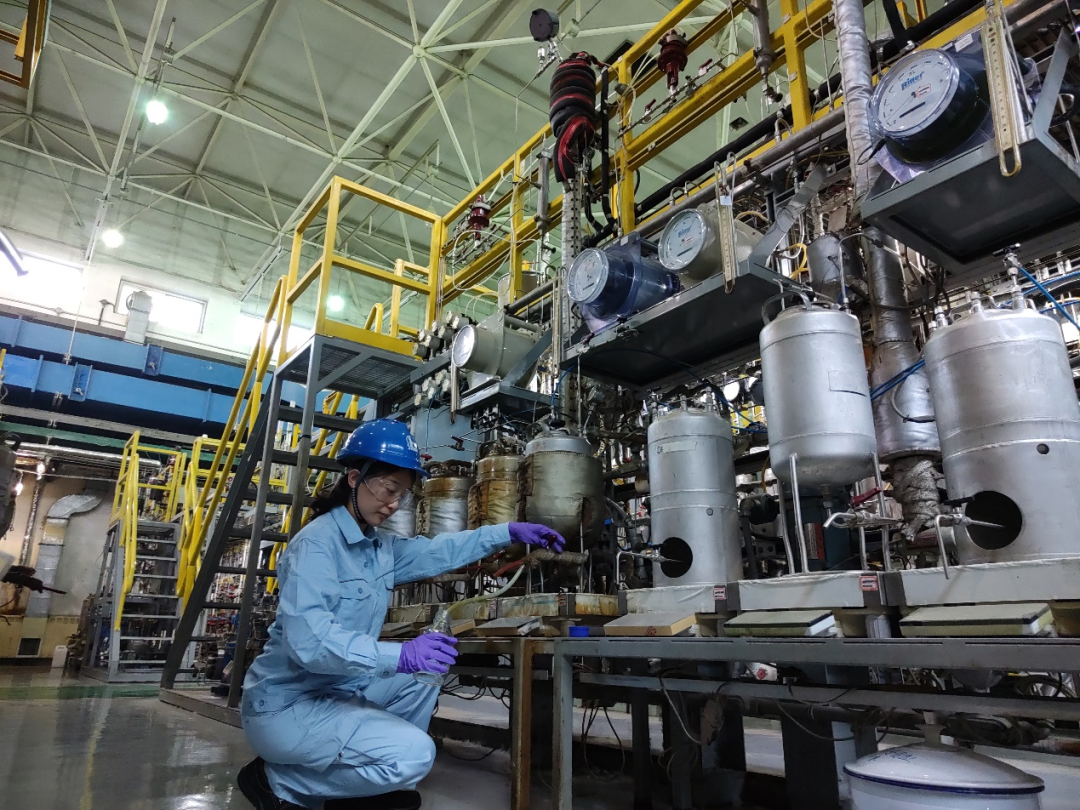
“每一个数据背后都是巨大的工作量。最终,我们花了近3年时间把一套1982年的老装置改造成生物航煤生产装置。”李成刚说。
“1号航煤”生产时,由于反应过于剧烈,加氢工艺温度上升速度很快超过范围。在场所有人高度紧张。“要不要暂停项目?”“时间和成本耗不起!”团队不断调整方案,终于克服了困难。
在镇海炼化生物航煤生产车间,这样的紧张局面随时可能出现。
“生产中的许多问题是实验室看不见的,出现问题必须有预案及时应对,不可能再回实验室去。”聂红感慨,“用不到10年时间实现生物航煤的规模化生产,确实是一件值得自豪的事。”
今年4月,镇海炼化生物航煤正式获得可持续生物材料圆桌会议认证颁发的RSB可持续认证证书,标志着我国生物航煤产品具备进入欧洲及国际航空减排市场资质。6月,我国首套生物航煤工业装置成功产出生物航煤。
在首都北京和东海沿岸,创新团队还在努力——降低生物航煤成本,提高产品收率,开发更高效低碳的生产技术。“我们要把生物航煤技术储备好,随时响应国家号召!”李成刚的话道出了中国生物航煤人的心声。
编辑:沈唯(实习)
审核:岳靓